Understanding Vacuum System Components for Efficiency in Business
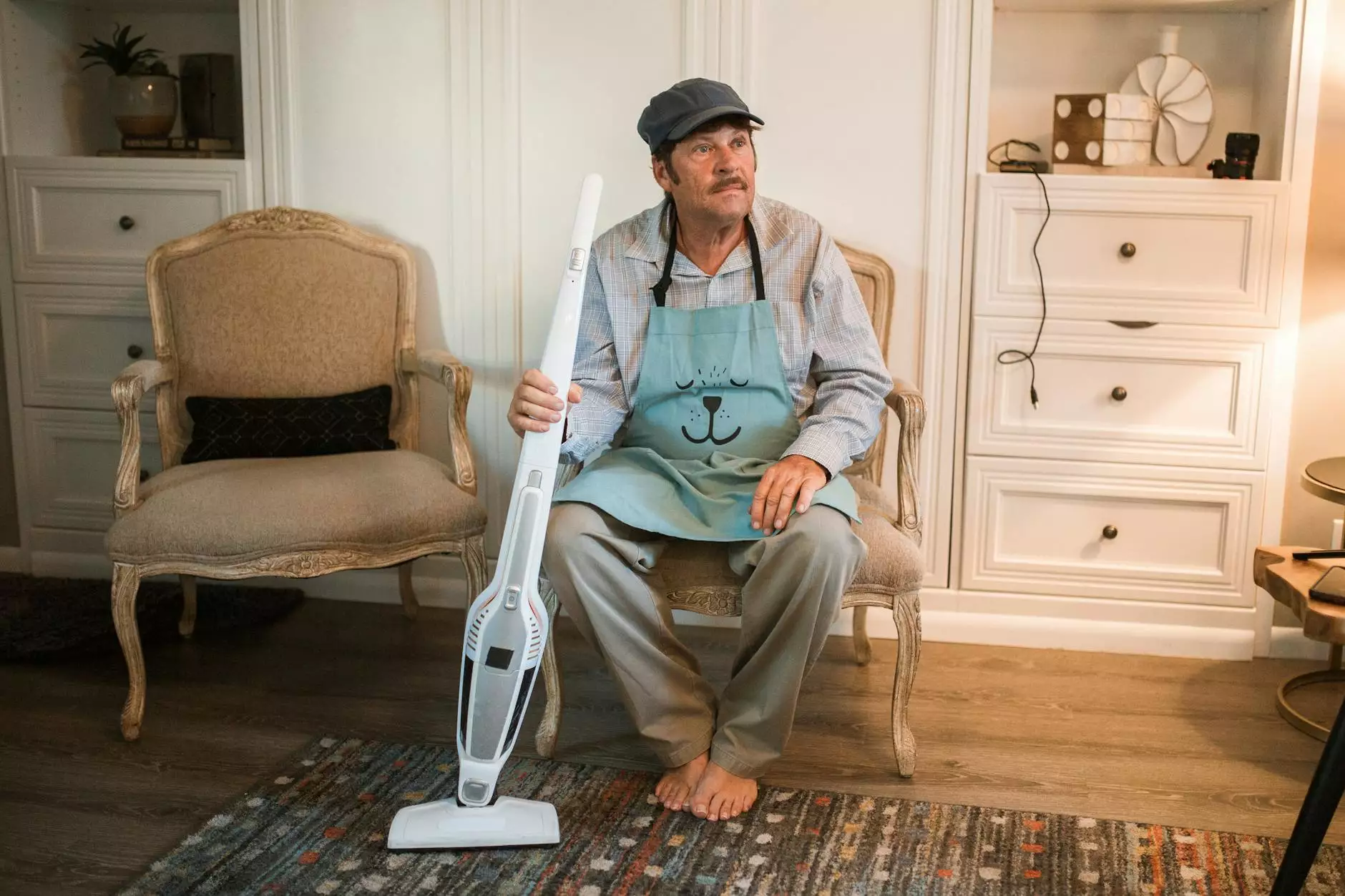
In the modern industrial landscape, the significance of vacuum system components cannot be overstated. These essential parts play a vital role in ensuring the efficiency and effectiveness of various processes across numerous sectors. From manufacturing to food packaging, understanding how these components work can lead to increased productivity and enhanced operational capabilities. This article delves into the intricate world of vacuum systems, covering their essential components and their critical applications in business.
The Basics of Vacuum Systems
A vacuum system is designed to produce a space devoid of matter, creating a vacuum environment for different applications. These systems are integral in facilitating processes where air or other gases could interfere with operations. The primary objective is to create a controlled environment where variables can be managed precisely.
The Importance of Vacuum Systems in Business
Vacuum systems are commonly employed in various industries, including:
- Manufacturing and Assembly: Precision components require vacuum systems to remove contaminants during production.
- Food Packaging: Vacuum sealing extends shelf life by removing air that leads to spoilage.
- Medical and Pharma: Sterile environments are maintained to ensure product integrity and safety.
- Electronics: Vacuum systems are crucial in the assembly of delicate electronic components, preventing damage from environmental factors.
Key Components of Vacuum Systems
Understanding the components of vacuum systems is essential for optimizing their functionality. Each element plays a specific role in creating and maintaining a vacuum. Below, we explore the critical components that make up these systems.
1. Vacuum Pumps
The heart of any vacuum system, vacuum pumps are responsible for extracting air and gases from a chamber to create a vacuum. They come in various types, including:
- Positive Displacement Pumps: These are ideal for applications requiring low or medium vacuum levels.
- Momentum Transfer Pumps: Also known as molecular pumps, they are suitable for achieving high vacuum levels.
- Entrapment Pumps: These pumps trap gases and vapors in a solid or liquid medium, important for ultra-high vacuum applications.
2. Vacuum Valves
Vacuum valves control the flow of gases within a vacuum system. They prevent backflow, isolate parts of the system, and ensure that the vacuum level is maintained. Various types include:
- Isolation Valves: These prevent the vacuum from leaking when a section of the system is opened.
- Throttle Valves: These are used to regulate the vacuum level, allowing for precise control.
- Check Valves: These allow airflow in one direction only, preventing backflow.
3. Vacuum Gauges
Vacuum gauges are crucial for monitoring vacuum levels accurately. Various types include:
- Mechanical Gauges: These use a mechanical mechanism to display the pressure level and are reliable for less demanding applications.
- Electronic Gauges: Providing digital readings, these gauges offer precision in high-tech environments.
- Capacitance Diaphragm Gauges: Ideal for ultra-high vacuum applications, they offer excellent accuracy.
4. Vacuum Filters and Traps
To protect vacuum pumps and maintain the integrity of the vacuum, filters and traps are utilized. They prevent contamination by removing particulates, oils, and moisture from the gas stream. Various filtration options include:
- HEPA Filters: Effective for trapping microscopic particles.
- Liquid Traps: Designed to capture vapors and liquids before they reach the pump.
- Oil Filters: These are crucial for preventing oil contamination in rotary vane pumps.
Applications of Vacuum Systems in Advanced Business Operations
Vacuum systems find applications in different fields, enhancing operational capabilities and driving efficiency. Here are some prominent applications:
Manufacturing and Assembly Lines
In manufacturing, vacuum systems streamline processes such as material handling and part assembly. Automated vacuum systems facilitate lifting and moving components without mechanical grip, minimizing damage and increasing speed. Several sectors rely on these systems, including automotive, aerospace, and electronics.
Food Industry
In the food industry, vacuum packaging is essential for preserving food quality. It prevents oxidation and microbial growth, ensuring products remain fresher for longer. As consumers increasingly demand convenience and quality, vacuum systems have become integral to the food supply chain.
Medical Applications
In medical and pharmaceutical applications, maintaining a sterile environment is critical. Vacuum systems are used in sterilization processes, ensuring that equipment and products are free from contaminants. Their reliability ensures patient safety and compliance with health regulations.
Research and Development
In R&D, vacuum systems support experiments requiring controlled environments. This is crucial for scientific discoveries and innovations across various fields, including chemistry, physics, and materials science. The ability to manipulate variables in a vacuum allows for precise and significant advancements.
Advantages of Implementing Vacuum Systems
Implementing vacuum systems offers numerous advantages that contribute to enhanced business performance:
- Increased Efficiency: Automation with vacuum systems reduces manual labor and speeds up processes.
- Cost Reduction: By minimizing waste and enhancing process reliability, businesses can save significantly on costs.
- High Precision: Vacuum systems provide precise control, allowing for consistent quality across production lines.
- Improved Product Quality: Maintaining a vacuum environment extends the shelf life and integrity of products.
- Compliance: Vacuum systems help businesses meet industry standards for quality and safety.
Conclusion
In conclusion, the role of vacuum system components in various industries is indispensable. These components form the backbone of efficient operations, contributing to improved productivity, product quality, and cost-effectiveness. Understanding the different components—from pumps to gauges—enables businesses to leverage vacuum systems effectively, ensuring they remain competitive in a rapidly evolving market. By investing in sophisticated vacuum technology, companies can drive innovation while maintaining quality and efficiency across their operations.
At TMM, we understand the importance of high-quality vacuum systems and their components in enhancing business efficiency. Explore our range of solutions tailored to meet your specific industry needs and discover how we can help your business achieve operational excellence.